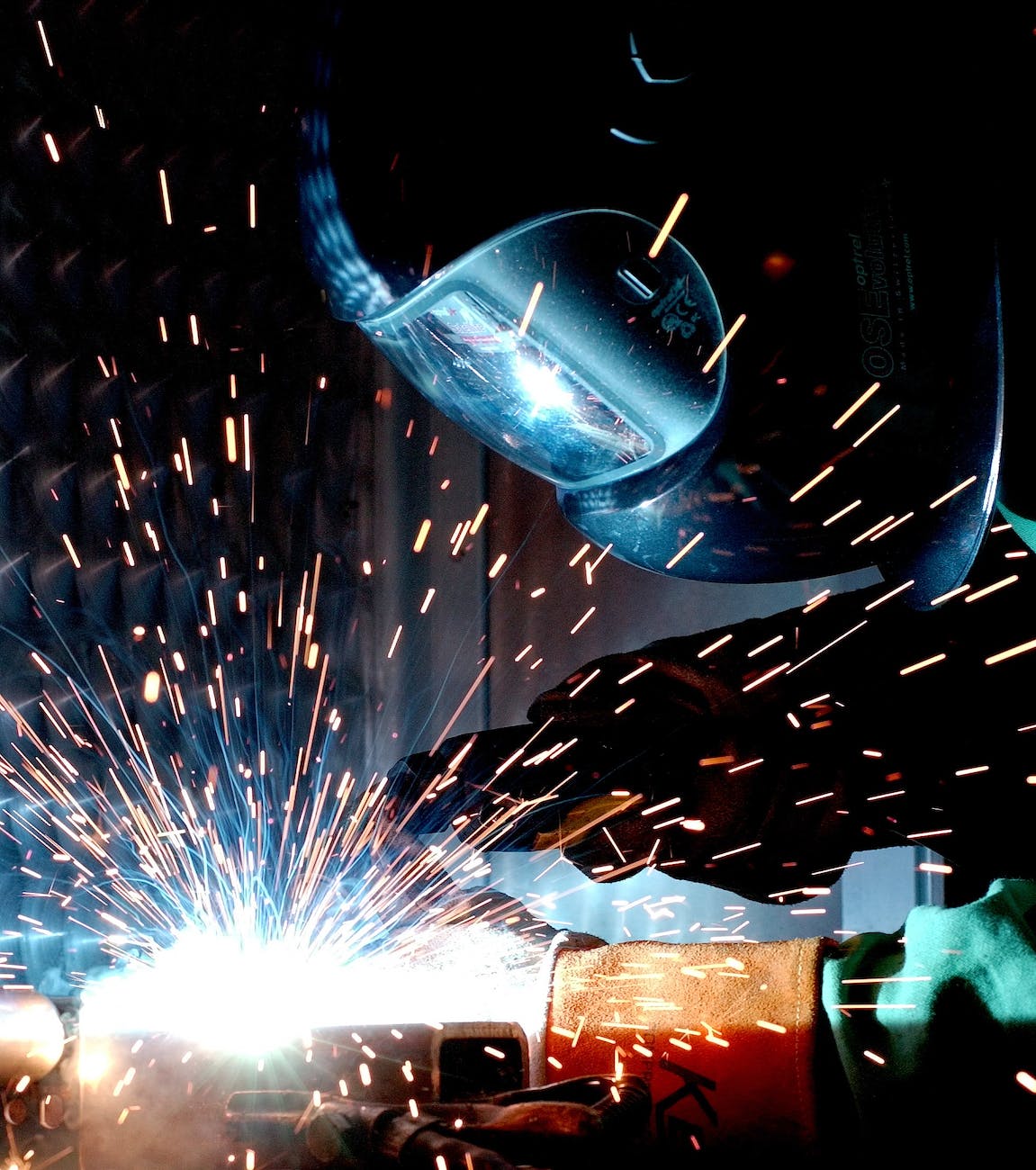
In a previous post, I explain the safeguard mechanism and the its recent changes.
In coming blogs I would like to explore some of the facilities covered by the safeguard mechanism, what they can do and what they are doing to comply with their obligations. I am going to work down the 2021 to 2022 reported safeguard facilities emissions data from highest to lowest skipping over the power stations subject to the Sectorial Baseline. I am also skipping over gas today because I want to write about steel.
Steel produces around 1.85 tonnes of carbon dioxide per tonne of steel produced and is mostly produced from the reduction of iron oxides, like Hematite, and for the provision of heat into blast furnaces.
Australia’s largest steel works is Bluesope’s Port Kembla Steel Works with reported safeguard emissions of 6.2 Million tonnes against a production adjusted baseline of 6.9 Million tonnes (2021 to 2022). By these numbers Port Kembla is already operating at a factor of 0.90, which, if these numbers are correct, holds their position until the 2024 to 2025 reporting year. However, come July 2025, they are going to have to make further improvements, or spend a few dollars on Australian carbon credit units.
The other Australian steelmaker on the list is Liberty Steel’s Whyalla plant with a calculated base line of 2.7 Million Tonnes of carbon dioxide per annum and reported emissions of 2.15 Million tonnes of carbon dioxide per annum. Whyalla is sitting at 0.80 and are therefore on track until July 2027 provided these numbers hold true.
What can a steel mill do?
For brown field plants, I would start with efficiency. In particular, the full oxidation and preferably monetisation of off gases from coke ovens.
You can also substitute hematite iron ore (Fe2O3) with magnetite iron ore (Fe3O4) to improve the iron to oxygen and therefore carbon dioxide ratio. This essentially reduces the emissions from reduction by 8/9th; however, magnetite ore tends to be lower grade than hematite ore, so it is a bit more expensive to process at the mine.
The next option is to use a combination of direct reduction and electric arc furnaces, which reduces the iron ore at temperatures below the melting point of iron, reducing the amount of energy required for reduction. The iron is later melted in the electric arc furnace, which would be powered from the sectorial baseline covered electricity industry.
You can also increase your feed of scrap recycled steel into the plant lowering the demand for reducing agents. However, there is a natural limit on the availability of scrap iron and scrap is cheaper than ore and coke, so you would use as much as you can in any case.
We then start to have more expensive options of either carbon capture or hydrogen reduction.
BHP, ArcelorMittal, Mitsubishi Heavy Industries Engineering and Mitsubishi have signed a collaboration agreement to pursue carbon capture storage in steelmaking. The agreement involves a trial at ArcelorMittal’s steel plant in Ghent, Belgium along with another site in North America. As far as I am aware there are no full scale carbon capture storage plants operating on blast furnaces at full scale yet, so it will be interesting to see how this trial goes (please let me know if you know of one).
A ‘hydrogen easy’ option is to blend small amounts of hydrogen either into an existing direct reduction plant a blast furnace. ArcelorMittal have trialled blending hydrogen into a direct reduction plant in Canada at 7 percent hydrogen, 93 percent natural gas for 24 hours. I’m not aware of a plant that is yet in commercial operation (again please let me know if you are aware of one).
A ‘hydrogen heavy’ option is to construct a direct reduction plant that runs on 100 percent hydrogen, such as the H2 Green Steel plant currently under construction in Boden, Sweden.
What are the Australian Steel mills doing?
Liberty Steel have committed to the construction of a direct reduction plant and electric arc furnace. The direct reduction plant will initially operate on natural gas and a blend of hydrogen with the hydrogen feed increasing as it becomes commercially available. Liberty Steel has also committed to achieving carbon neutrality by 2030.
Bluescope’s 2022 Sustainability Report commits them to carbon neutrality by 2050 and a 2030 target of 12 percent emissions reduction (let’s see what the 2023 report says in light of the Safeguard Mechanism). Bluescope have allocated $150M for climate projects over the next five years and committed to increasing use of scrap, undertaking research in the use of biochar as an alternative to coke and researching direct reduction of Pilbara iron ores. They are also installing a 10MW electrolyser for blending hydrogen into the blast furnace.
The future
It will be interesting to see how these technologies plan out and how the economics of each technology play out against each other and against the cost of ACCUs. Interesting times ahead.
About the Author
Andrew Murdoch is the Managing Director of Arche Energy and is is a long term energy industry participant, advisor and energy nerd.
Safeguard mechanism baseline decline rate (FYI)
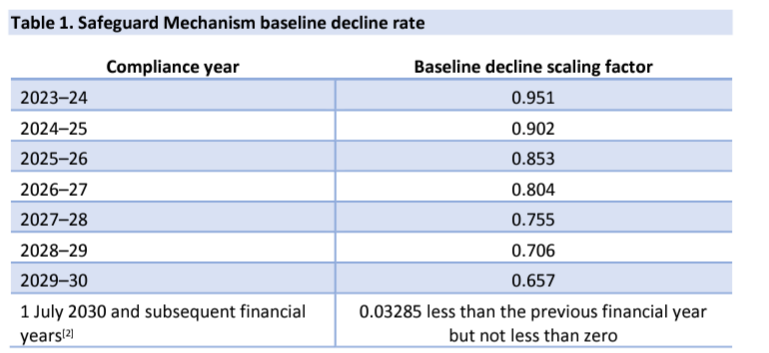